Shagun Polytech Pvt. Ltd.
About Us
We at Shagun Global, partake in diversified manufacturing activities in the field of Plastics boasting of 30+ years of experience. Under the able stewardship of Mr. Harish D. Yadav our mentor and founder we have been able to achieve organic but sustainable growth. Staying true to our organizational objectives of offering cutting edge expertise and quality products to our diverse clientele, we as an entity are synonymous to the best in the plastics industry in India. The group owes its continued success and growth to the enigmatic leadership of its founder and the hard work and quality centric efforts of its entire crew.
Charting our story from its early days, India at the beginning of the 90’s was opening its doors to global conglomerates; the local mat industry then was in its nascent stage heavily dependent on machines being imported from Japan. Importing Japanese machines exponentially increased the cost involved in setting up and managing the entire project. This made it prohibitive for entrepreneurial ventures to turn profitable and thus the growth of entire industry was contended.
We saw this as an opportunity to optimize business processes in this industry and decided to devout our heart and souls to this effort.
Identifying the need for better machines, spares, skilled labor which could be nurtured locally we got ourselves to the drawing board. Out of this effort was born the first locally produced Extrusion machine for hollow tubes required in the PP mat industry.
Since then we have played a pivotal role in this industry, from being manufacturer of machines to PP Mats (End Product) and exporting these from West Africa to South-East Asia. Building up on our expertise, In 2012, we started with PET Preforms manufacturing and have reached production capacity of 100 MT per month. PET Preforms are used predominantly in the beverage industry and we are continuously adding new SKU’s enabling us to provide better effective solutions to our customer.
We have formed strong relationship with our customers who have been with us for more than a decade. We are professional yet passionate towards our work, believe in mutually beneficial terms of business and ensure equilibrium towards stakeholders in today’s dynamic business environment.
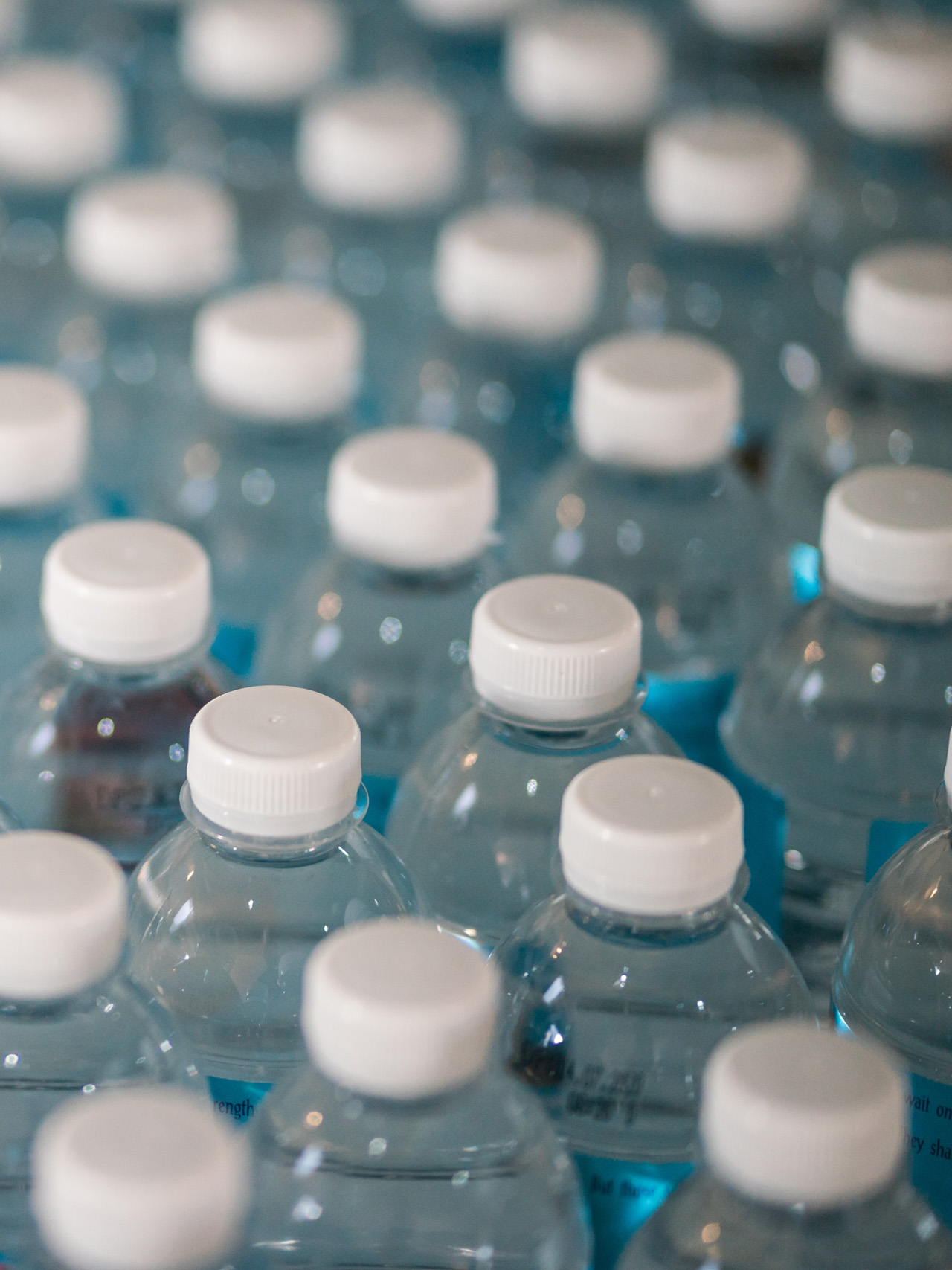
66% of energy is saved when producing
new plastic products from recycled materials instead of raw (virgin) materials.
Drippers
Designed in Israel, Shagun drippers are being proudly manufactured in India since 2014. To ensure highest quality, the drippers are manufactured on Imported hot runner moulds using high speed injection moulding machines. Before being box packed, fully automated material handling, vision sorting machines weed out half shots and flashed drippers to ensure safety and integrity of each dripper. With Shagun drippers, what you get is a product of highest quality and an unparalleled performance because of.
- Fine Mesh - first line of defense not allowing particles to enter and clog the line
- Higher Width Labyrinth - equal and easy flow of water at both ends with no jetting effect
- Whirling Effect - the labyrinth design ensures better pressure and velocity of water
- UV Stabilizers - ensure uniform master batch coloring making the dripper visible while punching
- High quality materials blend - ensure perfect bonding to the pipe
- Exceptional design - results in less chances of clogging with a self cleaning mechanism and higher life ceiling
- Round 12, 16 and 20 mm drippers available
- All drippers (Flat and Round) are sorted using vision inspection machine
Download Brochure
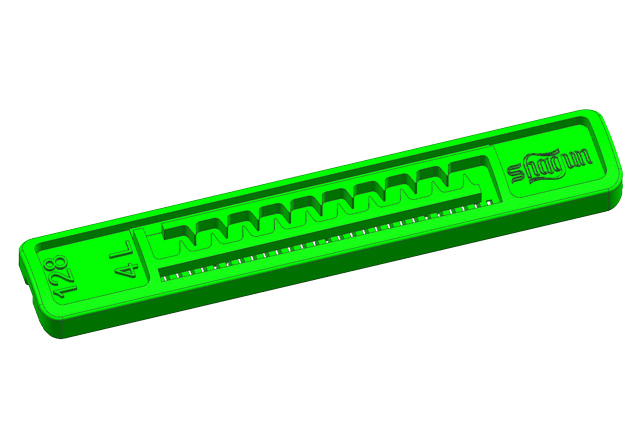
DRIPPERS
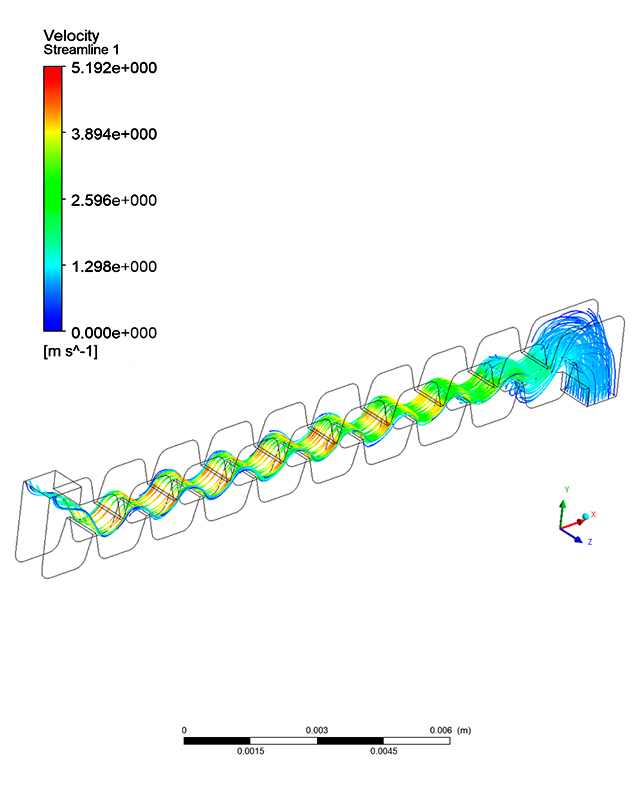
STREAMLINE
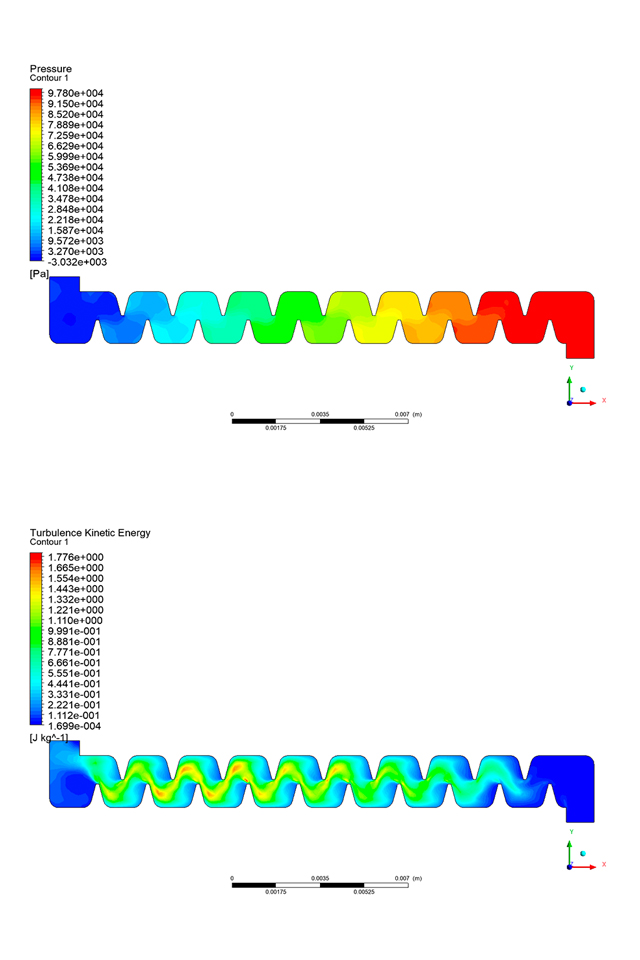
PRESSURE & TURBULANCE
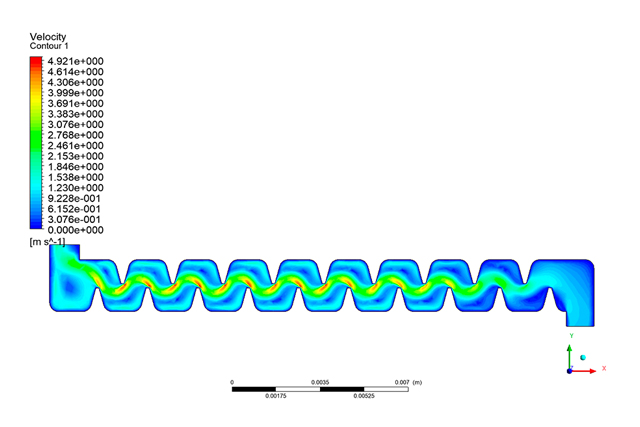
VELOCITY
PET Preform
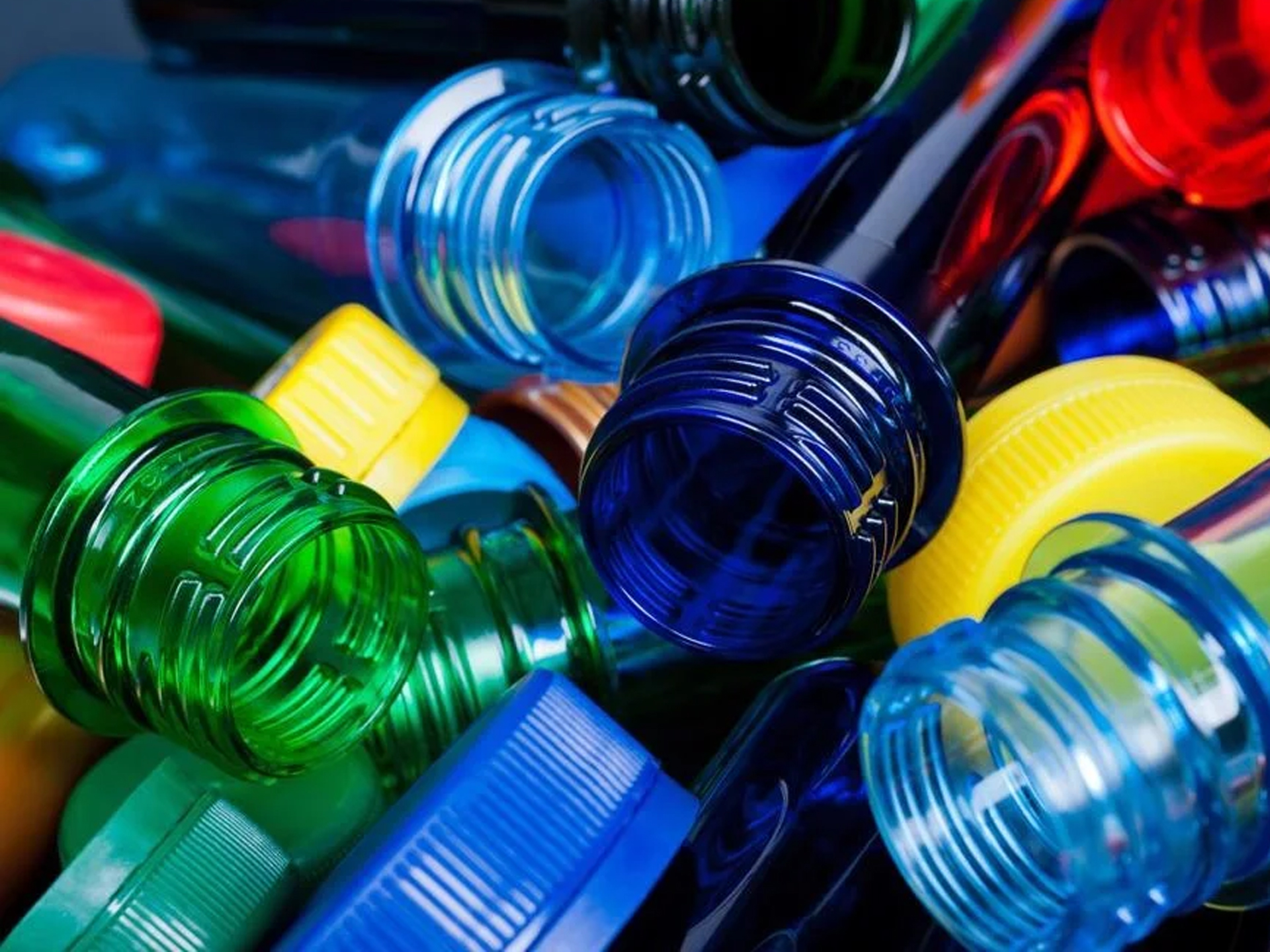
Shagun Polytech Pvt. Ltd., started in 2012 with single machine and ancillary, a dream to excel and focus , has grown till date to incorporate a total of five machines and a range to cater to diverse customers. PET Preform is the world's packaging choice for many foods and beverages because it is hygienic, strong, lightweight, shatterproof, and retains freshness. It is most commonly used to package carbonated soft drinks and water.
With an industry leading experience of handling and processing different plastics and polymers, We bank on our stringent control over the process and experience processing Polymers and Polyester. Our preforms have strength, thermo-stability, and transparency achieved by close loop feedback automation in the entire process including our machine, moulds and ancillaries. We cater to diverse customers in Water, CSD and confectionary industry and are a reliable partner in the supply chain.
We understand our customer’s need of quality and timely delivery and are committed to deliver the same using the best material selection, precise monitoring of process parameters. Our growth is evident from repeat orders and continuous cordial relation we enjoy with our customers. With precise finish, uniform wall thickness of preforms and happy customers, the blown bottles (and Jars) are testimonial of our efforts itself.
Download SKU
Quality
Assurance Plan
- A Preform lab is set up to check the dimensional accuracies & other acceptance criteria such as Flash, Sink Marks, Ovality, short shot to help bottlers avoid line rejections
- For AA levels, we get periodical test done at lab of Reliance Industries
- Periodical calibration of weighing scale to ensure precise delivery weight
- Preventive maintenance plan for machine and mould to avoid break downs & smoother running of the system
- Polariscope
- Micro Weighing Scale
- Preform thickness tester
- Go & No Go Gauges for Perform
- Digital Vernier Caliper and many others…
Achieved in Accordance With
Raw Materials:- Tested in accordace with norms for PET Preforms
- Preforms are manufactured with Ferromatik Milacron machines and all the ancillaries from Nu-Vu Coanir
- No Human touch while manufacturing ensuring no contamination, hygiene and product finish
- Low AA content
- No Human touch while manufacturing
- Uniform wall thickness
- Accurate Thread & Neck Finish
- Standard Length
- Standard Body Diameter
- Excellent Surface Finish
- Aesthetically and technically at par with best in class systems
Facts PET Recycling

- In the mid-1940’s DuPont chemists searching for materials for use in textile fibers synthesized PET
- In the early 80’s, recycling of post-consumer plastic packaging began as a result of individual state bottle deposit programs
- According to the ACC, 94% of Americans have access to a plastics recycling program (2014). Most curbside collection programs collect more than one type of plastic material or resin which usually includes PET and HDPE
- Since 1977, the ACC has found that the 2-liter soft drink bottle has gone from weighing 68, to just 47 grams saving more than 180 million lbs of packaging in 2006 due to lightweighting
- The EPA states that in 2012, the US produced approximately 14 million tons of plastics for packaging and containers. Specifically 31% of PET bottles and jars were recycled
- The APR states that in 2012, 5.5 billion lbs of PET could be found on US shelves with 1.7 billion lbs recycled. Of the 5.5 billion lbs, 326 million lbs were from post-consumer recyclate
- NAPCOR states that a cubic yard of landfill space is conserved by recycling the equivalent of 2,430 2-liter plastic PET bottles. In addition, the EPA states that 12,000 BTU’s can be saved by recycling 1 lb of PET
- NAPCOR’s Life Cycle Inventory data indicates for a single lb of PET flake utilized, energy usage and greenhouse gas emissions are diminished by 84 and 71% respectively
- Over 85 bottles can be used to make filling for a sleeping bag according to the APR. NAPCOR states that the average American household used roughly 42 lbs of PET plastic bottles in 2005
- More than 50% of the word’s synthetic fiber is produced from PET
- 66% of energy is saved when producing new plastic products from recycled materials instead of raw (virgin) materials
- Film was created in the 1950’s by stretching a thin extruded sheet of PET which is found today in photographic, video, X-ray and packaging films
- In the 70’s blow-stretch molding of PET in shatterproof bottles was developed
- A recycling mill in PA begins accepting residential plastics in 1972
- In 1977 the first PET bottle was recycled
- Major US cities in the 80’s begin establishing curbside pick-up programs
- In 2001 major recyclers embrace single stream recycling which dramatically increases the recycling rate of various recyclable material
- Today PET is the #1 most commonly recycled material with a growing number of consumers and reclaimers recycling PET thermoformed packaging
- At least 90 percent of the price of a bottle of water is for things other than the water itself, like bottling, packaging, shipping and marketing
- PET plastic can be recycled into: clothing, fiberfill for sleeping bags, toys, stuffed animals, rulers and more